Applications of computer software known as Manufacturing Execution Systems (MES) are used in manufacturing companies to oversee and control the production process. It is a real-time system that provides assistance for the manufacturing process by delivering information that is accurate and timely to the appropriate individuals at the appropriate moment. This enables those individuals to make choices that are informed and help improve the production process.
The Manufacturing Execution System (MES) was developed to assist in the administration and control of critical production processes, such as the management of raw materials, production planning and scheduling, and process control. It helps manufacturers to monitor, manage, and optimize the manufacturing process so that they can fulfill the intended objectives of quality, cost, and delivery. It offers real-time insight into production activities.
The shop floor is often the location where MES software is installed in order to offer real-time data on production processes. This data may include information regarding raw materials, work in progress, completed items, and production activities. Additionally, the program offers capabilities for monitoring and regulating the production process, such as machine usage, downtime, and maintenance. Additionally, the software offers help for decision-making in the form of reports, alerts, and analytics.
The primary objective of MES is to eradicate the disconnect that exists between the planned and actual carrying out of the manufacturing process. The Manufacturing Execution System (MES) offers a real-time view of production operations, which enables manufacturers to monitor and control the production process, identify and resolve issues before they become problems, and optimize the production process in order to meet the desired goals of quality, cost, and delivery.
The Value of the MES
MES helps to identify areas of the production process that can be improved by providing real-time data about production operations. This enables manufacturers to make informed decisions that optimize production efficiency and reduce waste, which ultimately results in improved production efficiency.
MES delivers real-time data regarding production processes, which enables manufacturers to monitor and manage the production process and make informed choices that optimize the manufacturing process. This results in better decision-making.
MES delivers real-time data regarding production activities, allowing firms to monitor and manage the production process to guarantee that items are made to the necessary quality standards. This results in improved product quality.
MES gives a real-time picture of production processes, which enables manufacturers to monitor and manage the production process and spot anomalies before they become problems. This increased visibility into production operations is one of the primary benefits of MES.
Because MES delivers data in real time regarding production activities, it enables manufacturers to improve their ability to communicate with customers, suppliers, and other stakeholders on the state of the production process.
Manufacturing execution systems (MES) make it possible for different departments and teams working within a manufacturing organization to work together in a more efficient manner by providing a shared view of production operations and making it possible for better communication and coordination.
Principal Constituents of the MES
Production Data Management: MES delivers real-time data on production activities, including data about raw materials, work in progress, completed items, and production procedures. Production Data Management is also known as M.E.S. (Manufacturing Execution System).
Management of the Production Process: MES offers tools for monitoring and regulating the production process, including equipment usage, downtime, and maintenance. Production Process Management
Production Planning and Scheduling: The Manufacturing Execution System (MES) lends a hand to the process of production planning and scheduling by giving manufacturers access to data in real time regarding production operations. This gives manufacturers the ability to make decisions that are both informed and beneficial to the production process as a whole.
Quality Management: MES provides real-time data about production operations, which enables manufacturers to monitor and control the production process in order to ensure that products are manufactured to the desired quality standards. This helps manufacturers meet customer demands for higher product quality.
Supply Chain Management: The Manufacturing Execution System (MES) delivers real-time data regarding production processes, which enables firms to better monitor and manage the production process, as well as increase communication and collaboration with customers and suppliers. Supply Chain Management (SCM)
Putting in place a MES
In order to successfully implement MES, one must have a thorough understanding of the production process as well as the objectives of the manufacturing organization. The first stage in installing MES is to conduct an analysis of the existing manufacturing process and identify the areas in which MES is likely to be of the most assistance. In order to accomplish this, it may be necessary to collaborate with key stakeholders in the manufacturing organization, such as production managers, quality control personnel, and IT staff, in order to gain an understanding of the manufacturing organization’s current production process and its goals.
After the evaluation is over, the following step is to choose a MES software solution that is appropriate for the needs of the business. There is a wide variety of MES software solutions on the market today; nevertheless, it is essential to choose one that caters to the particular needs of the manufacturing firm. When selecting a software solution for MES, some of the factors that should be taken into consideration are the program’s degree of customization, scalability, compatibility with already existing systems, and simplicity of use.
After a Manufacturing Execution System (MES) software solution has been chosen, the subsequent stage is to put the software into operation and to integrate it with the many other systems that are used by the manufacturing company. It is possible that this will need staff to be trained on how to operate the new system, as well as the update of any current systems or the installation of new hardware and software.
After it has been implemented, the Manufacturing Execution System (MES) need to be routinely examined and upgraded so that it can continue to cater to the ever-evolving requirements of the manufacturing organization. This may need the addition of new features, updates to already implemented functions, or integration with other systems depending on the requirements.
In conclusion, Manufacturing Execution Systems, often known as MES, play an essential part in the management and control of the production process inside a company that specializes in manufacturing. MES assists manufacturers in the monitoring and control of the production process, the detection and resolution of issues before they become problems, and the optimization of the production process to meet the desired goals of quality, cost, and delivery. MES does this by providing real-time data about production operations.
The implementation of MES involves careful planning and consideration of the particular requirements of the manufacturing organization, as well as a commitment to routinely evaluate and update the system to ensure that it continues to satisfy the requirements of the manufacturing organization. When firms have the appropriate MES system in place, they have the ability to greatly increase the effectiveness, quality, and competitiveness of their production processes.
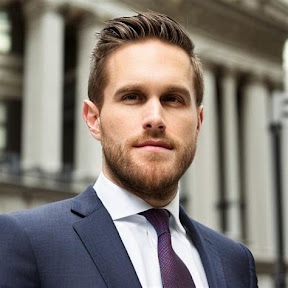
Darren Trumbler is a versatile content writer specializing in B2B technology, marketing strategies, and wellness. With a knack for breaking down complex topics into engaging, easy-to-understand narratives, Darren helps businesses communicate effectively with their audiences.
Over the years, Darren has crafted high-impact content for diverse industries, from tech startups to established enterprises, focusing on thought leadership articles, blog posts, and marketing collateral that drive results. Beyond his professional expertise, he is passionate about wellness and enjoys writing about strategies for achieving balance in work and life.
When he’s not creating compelling content, Darren can be found exploring the latest tech innovations, reading up on marketing trends, or advocating for a healthier lifestyle.