Managing warehouse inventory, or inventory in general, can be challenging. Failure in inventory management can lead to chaotic situations in your warehouses that can cause a disturbance in the entire supply chain. Improper management will turn your assets to liabilities.
In these days where the distribution market is competitive, it is imperative that you do not lose money over an integral part of your business. To avoid financial losses, you must know what are the detrimental ways of inventory management and remove them if they exist at your warehouses.
Here are the worst warehouse inventory practices and how to avoid them:
Manual inventory taking and stocktaking
As your company grows lack of automation can make your inventory process error-prone. Manual processes in warehouses can be considered trouble because it does not only cost you time, it can also inflict damage financially.
How to avoid: Managers need to automate. The latest technology in warehouse management is more accurate, efficient and most of all, reliable. Reliability, in this case, is of emphasis. Having an automated system also addresses planning because you can use collected data to forecast and proactively plan for the future. It also helps with problems like overselling items in stock.
Disorganization
Disorganization is one of the biggest enemies of efficiency and productivity. If your warehouse is not properly organized, it negatively affects not only inventory management but warehouse management as a whole.
How to avoid: Optimize. Keep in mind that having an organized inventory is key to saving time, efficiency, and fulfilling more customer orders, productivity. A great exhibit of an optimal facility is an LSCR warehouse.
Spreadsheets/lack of forecasting
Using a spreadsheet program to manage your inventory can quickly lead to severe issues. This method does not provide customer demand visibility, which causes excessive inventory and weak customer responsiveness, which impacts reorder points, another important factor of inventory management.
How to avoid: Time-phased inventory planning. A company must know not only what is needed at the present, but also what will be needed in weeks in terms of inventory.
Managing items the same way
Presuming that every item you sell is consumed the same way is a mistake. This mindset can lead to having no stock of one item while having excess stocks of another.
How to avoid: Utilize safety time rather than safety stock. Safety time automatically brings up safety stock to anticipate demand of a certain item, while safety stock is stagnant that must be manually set and does not account for any changes in demand.
Not engaging customers
Customer engagement also plays a factor in distribution. Not knowing the “mood” of your customer base also impacts your inventory planning. Using unplanned resources can kill the profit margin of unexpected sales.
How to avoid: Listen to your customers. Use methods of gathering feedback and data if you must (i.e. surveys).
Lack of evaluation
In order to know if your inventory management system or any system is effective, you must perform an evaluation. Performance measurements are key to determining what needs to be changed and what can be retained.
How to avoid: Set up a performance review process. Be sure that it is unbiased and covers everything that has to be looked at in your inventory management system.
To summarize, your warehouse operations must always practice healthy inventory ways to maintain good income and prevent any unwanted losses.
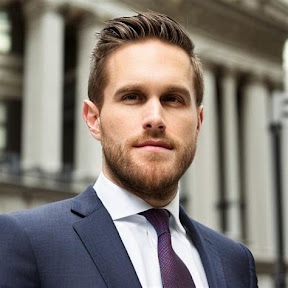
Darren Trumbler is a versatile content writer specializing in B2B technology, marketing strategies, and wellness. With a knack for breaking down complex topics into engaging, easy-to-understand narratives, Darren helps businesses communicate effectively with their audiences.
Over the years, Darren has crafted high-impact content for diverse industries, from tech startups to established enterprises, focusing on thought leadership articles, blog posts, and marketing collateral that drive results. Beyond his professional expertise, he is passionate about wellness and enjoys writing about strategies for achieving balance in work and life.
When he’s not creating compelling content, Darren can be found exploring the latest tech innovations, reading up on marketing trends, or advocating for a healthier lifestyle.