Occupational Health and Safety is an important part of any workplace as it ensures the wellbeing of the employees within the organization. In order to ensure that companies maintain a high standard of health and safety the Occupational Safety and Health Administration conducts inspections on companies.
Who is OSHA?
OSHA is the Occupational Health and Safety Administration, an organization within the Department of Labor, that created the Occupational Health and Safety Act in order to ensure safe working conditions for employees by producing a set of rules and standards for companies to abide by.
What is an OSHA inspection?
Inspections are a responsibility undertaken by OSHA to achieve health and safety for the millions of workers employed by companies under their jurisdiction. To ensure efficiency these inspections are prioritized under the following categories.
- Imminent danger situations – Potentially hazardous situations that can cause harm or major injuries.
- Severe injuries and illnesses – Work related injuries that lead to hospitalization E.G. the loss of a limb.
- Worker complaints – Complaints from employees or anonymous whistleblowers
- Referrals – Referrals from other federal agencies, companies, groups or individuals.
- Targeted inspections – Inspections aimed at highly hazardous industries such as construction companies.
- Follow up inspections – Conducted to ensure corrective measures have been taken.
You might also like to read: THE BEST FACILITY MANAGEMENT SOFTWARE REVIEW FOR SMALL BUSINESSES
A company does have the authority to go to a court of law and seek an inspection warrant to be issued by OSHA before an inspection can take place.
OSHA does not generally provide advanced notice of their inspection to a company unless it is due to one of the following reasons.
- Imminent danger that the company can correct.
- When special preparation is required.
- If the inspection is to occur outside of the company’s operating hours.
- If the company’s management is not based on the site and requires advanced notice to be present.
What are the 3 parts of an OSHA inspection?
The three segments of the OSHA inspection are as follows:
- The Opening Conference
This is the first step in the safety inspection process, the safety inspector issued by OSHA will arrive at the company’s office or facility and explain the purpose of the inspection to the manager in charge as well as a representative of the employees. While this is a brief step it is extremely important as the inspector will explain the hazards they will be looking out for.
It is during this phase that the inspector will request the companies occupational injuries and illnesses logbook and summary of the possible hazards that have been corrected, this is a compliance requirement.
While these records can be provided in the form of logbooks and spreadsheets, technological advancements have been made and many companies have adopted a cloud based health and safety record keeping application to ensure compliance. These software applications streamline incident reporting and maintain accurate records compiled by the company.
Once the records have been reviewed and the inspector deems the records to be compliant thus far the second step will begin.
- The Walkaround
In the case of an employee complaint the second step in the inspection will consist of the inspector, company manager and employee representative addressing the possible hazard.
The inspector will then expand their search and conduct a more thorough investigation that will cover the whole workspace.
It is during this period that the inspector will conduct private interviews with the employees, these interviews remain confidential. It is not uncommon for inspectors to conduct private and confidential interviews with employees outside of the workplace. This is done in order to encourage workers to express their views on the health and safety within their company and share any past incidents that may have occurred.
During the walkaround stage inspectors will test machinery, inspect equipment such as personal protective equipment and conduct measurements such as noise levels, dust levels, temperature and any other possible variables that can affect an employee who will be exposed to it.
The walk around stage can take many hours or even days to complete with inspectors coming back to view operations during different shifts in order to gain a thorough understanding of the health and safety standards.
You might also like to read: TOP 10 BEST EHS INCIDENT MANAGEMENT SOFTWARE FEATURES
- The Closing Conference
This is the third and final part of the inspection process. Safety inspectors are required to hold a closing conference, while these can be handled jointly they will often be conducted separately with employees being addressed first to allow for further employee input.
During this conference an inspector will address the hazards found, the corrective measures that must be taken and the penalty if these hazards have not been corrected within the period of time allocated. The penalty will be in the form of a citation or financial penalty.
A company does have a right to contest the findings of the inspection if they do not agree with the results provided during the closing conference, they may also contest the length of time allocated for corrective measures, however the findings must be contested within 15 days of receiving the report.
There are many factors to take into consideration when your company is undergoing an inspection. The priority should be the health and safety of the employees as well as compliance with the rules and regulations put in place.
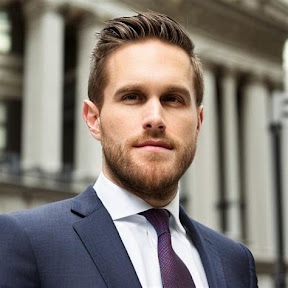
Darren Trumbler is a versatile content writer specializing in B2B technology, marketing strategies, and wellness. With a knack for breaking down complex topics into engaging, easy-to-understand narratives, Darren helps businesses communicate effectively with their audiences.
Over the years, Darren has crafted high-impact content for diverse industries, from tech startups to established enterprises, focusing on thought leadership articles, blog posts, and marketing collateral that drive results. Beyond his professional expertise, he is passionate about wellness and enjoys writing about strategies for achieving balance in work and life.
When he’s not creating compelling content, Darren can be found exploring the latest tech innovations, reading up on marketing trends, or advocating for a healthier lifestyle.
2 thoughts on “What are the 3 parts of an OSHA inspection?”