The success of the business comes first when the operational activities are efficient. Current businesses are optimizing their operations through efficient work order management systems. As a leader, you must be concerned with the capabilities of your maintenance solution rather than monitoring individual teams’ performance. Maintaining tons of paper works make things more complicated and time-consuming. Thus, using Computerized Maintenance Management System (CMMS) is perfectly a good reason and surprisingly 37% of organizations are looking to increase their investments into it. To achieve proactive operations, the primary step of a frontrunner should be reducing the impact of maintenance-related issues to eliminate workplace stress. Here I am about to mention seven best reasons to prevent paper-based management systems and begin the use of CMMS to extend operational excellence at your organization.
1. Efficiency in Managing Operational Excellence
At first, ask yourself how paperless is your current management system? I am pretty sure that your desk is still piled up with printed work orders and lots of other paper works. Isn’t it difficult to find the correct paper within short notice? Yes, it is! Why don’t you create a system in place that will help you to track, create, edit and communicate to your team without the touch of a paper? By using CMMS, you are not only reducing time and use of paper, but you are also reducing your cost of operation across your whole maintenance department. The proper implementation also ensures the maintenance of the company’s assets and working efficiently.
You might also like to read: Top 5 Support Process Automation Apps to Improve Business Productivity
2. Vendor, Inventory and Asset Management
Through CMMS software, being a vendor or employee you can request work orders from any part of the world. This streamlined solution saved a lot of costs too. In manufacturing companies, CMMS can catch the patterns of material consumption and adjust supply ordering accordingly to optimize stock levels. It will help you to get rid of costly human error through automated tracking mechanisms. Having access to the complete work history of equipment and machines is one of the staples of computerized maintenance management systems.
3. Improving Workflow
Imagine the life of a manager who is in charge of several regions and multiple facilities. Every day following up with the line managers for getting updates and manually maintaining the team for achieving the company goal is too tiring and chances of missing updates are low. There will be days during the seasonal business that the manager will have an unproductive day with lots of mistakes. CMMS will automatize a significant part of repetitive tasks, speed-up the communication between the upkeep team keeping them on constant page. Managers can swiftly change work importance, work orders, and due dates and communicate them quickly to the total team with the assistance of CMMS.
4. Understanding and Forecasting Future Needs
A data-driven company can foresee the future and take proper precautions before any disasters arrive. As a manager, your top priority is to protect the organization from unforeseen dangers. The wide spectrum of knowledge in your CMMS of your inventory can assist you perceive your future wants so you’ll be able to properly organize and modify your maintenance operations.
5. Easily Changing Work Priority and Assignments
Suddenly you saw that the workers are striking and manufacturing stopped! Instead of calling everyone over the phone and assigning tasks to solve the problem is very time-consuming. You can easily inform everyone about the changes of plan through maintenance software and reassign the task within a very short period of time which will
both save time and money. Quick communication while changing assignments and work priorities improve work efficiencies and CMMS can easily do that with fast response time too.
6. Improving Response Time
The biggest advantage while using CMMS is that you can use it from your mobile device too. If any of your team members are sick and cannot have access to a laptop or desktop then they can respond to their task very easily from their mobile phone by just lying on the bed. Through CMMS, anyone from the app can send comments or pictures
of the work order easily to the supervisor by increasing response time. The response time can be increased through malfunction alert and push notifications too. Such fast response time can result in saving money at the end of the year.
You might also like to read: HVAC System Maintenance for Commercial Properties
7. Reporting and Tracking
While using CMMS, you will notice a sheer amount of tracking data and reports which will seem very important to make your next technologyness. It is something that was impossible for you to notice or track while using manual paper-based or excel based management systems. Main goal of CMMS is to transfer this data into meaningful insights that lead to informed technologynesss and better business results. Through data analysis of CMMS, you can find out your average time to repair (MTTR), the average time between failure (MTBF), maintenance trend, and eliminate preventive maintenance waste.
Key Takeaways
By this time you already understood that by using CMMS you will get certain advantages which will help you organization and also professional goals to achieve. CMMS solutions bring numerous benefits with solid foundations. To summarize:
- You and your organization will save a lot of time and focus on the next big challenge.
- It will help you to go paperless and save trees.
- Your data will be safe and you can analyze them to find future opportunities.
- You can save lots of money and invest them in your next big project.
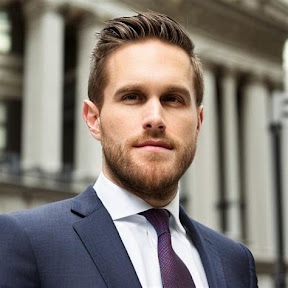
Darren Trumbler is a versatile content writer specializing in B2B technology, marketing strategies, and wellness. With a knack for breaking down complex topics into engaging, easy-to-understand narratives, Darren helps businesses communicate effectively with their audiences.
Over the years, Darren has crafted high-impact content for diverse industries, from tech startups to established enterprises, focusing on thought leadership articles, blog posts, and marketing collateral that drive results. Beyond his professional expertise, he is passionate about wellness and enjoys writing about strategies for achieving balance in work and life.
When he’s not creating compelling content, Darren can be found exploring the latest tech innovations, reading up on marketing trends, or advocating for a healthier lifestyle.