Due to the many unforeseen and volatile events that occurred in 2020 a renewed focus has been placed on safety management within the workplace. This is particularly relevant within large corporations where efficient facilities management is extremely important. The question is why is safety management so important and who is responsible for implementing it within a facility.
Safety Management is upheld by a Safety Manager. The reason for the focus on safety management is due to the benefits a company’s facility can gain from it, such as protecting the employees and assets, enhancing the reputation of the company, ensuring compliance and minimizing the risk of a compliance violation which could lead to a hefty fine.
What is a safety manager?
A safety manager is an employee who is qualified and specializes in the health and safety sector, they are tasked with developing and enforcing occupational health and safety regulations according to the legal guidelines provided by a countries Occupational Health and Safety act governing body.
While the roles and responsibilities of a safety manager changes to meet the varying needs of companies the following is a core overview of their role within a facility management context. These responsibilities listed are in place to minimize the possibility of risks and injuries occurring to an employee within a company’s facility.
Ensuring efficient management of the facility
It is simple, risk management cannot be implemented in a dysfunctional facility. Unexpected situations often leave facilities open to a certain level of danger, therefore managing a facility at its optimum capacity often ensures that employees understand their roles and how to operate safely and efficiently.
While facility management is not the sole focus of a safety manager, their assistance, alongside the implementation of smart tools such as Facility Management applications, can assist the facility manager in maintaining an efficient management structure.
Implementing a Facility Management solution assists in ensuring productivity, thereby ensuring safety. The advancement of applications such as Facility Management allows managers to monitor the processes carried out within the facility, this ensures that processes are carried out in a safe and efficient manner.
You might also like to read: How to become a good facility manager?
Developing Safety Standards
Often seen as one of the most critical responsibilities held by a safety manager, this role includes the following aspects.
-
Conduct occupational health and safety audits.
While this is often a task undertaken by occupational health and safety bodies, such as OSHA and NEBOSH, audits must be regularly undertaken by safety managers. Audits involve managers inspecting the current state of the facility, the processes, assets and equipment that can pose a threat to the health and safety of employees. Understanding the state of a facility allows managers to pinpoint points that need to be improved.
-
Developing occupational health and safety plans.
This stage often involves monitoring the processes within the facility and then developing systems and standards with clearly defined rules and regulations that minimizes the potential for risks or harm. During this stage assets will undergo maintenance in order to operate safely.
-
Train employees.
Safety plans will be reviewed by a company’s leadership, as gathering information from a number of employees will provide safety managers with increased insight, however once this has been completed it is the safety managers responsibility to train employees on what is considered acceptable standards and best practices. Regular communication and annual updates will be held by the safety manager in order to keep the staff up to date on the current safety standards.
-
Conducting realistic safety exercises.
Once a safety manager has completed an audit, developed a safety plan and trained the employees they will usually conduct a variety of safety exercises. The aim of these exercises is to understand the effectiveness of these processes put in place and pick up on any hazards that were unidentified during the audit. This stage can also be used to refine processes to best suit the staff.
Implement Safety Standards
Once the development and testing of safety standards has been completed the second segment of responsibilities held by a Safety Manager is the implementation phase.
-
Implement a health and safety plan
An effective safety plan often identifies and minimizes most of the possible safety hazards brought to the safety managers attention. The safety manager will now begin to implement the safety plans developed. This often ranges from posting clear signage and labels to the removal of inefficient work stations that can be an ergonomic hazard.
-
Provide employees with the correct equipment.
With high powered machinery, tripping hazards, dangerous chemicals and unsafe fumes often found present, the number of hazards found within facilities can be overwhelming. Safety managers therefore need to ensure that employees are equipped with personal protective equipment, this can often be the difference between employee safety and a potentially deadly incident.
You might also like to read: 200 Corporate Employee Wellness & Engagement Ideas For Productivity
-
Maintain and ensure compliance
Once the safety plan has been implemented there is now a program in place to maintain compliance, there must be solutions in place to ensure compliance is upheld. Occupational Health and Safety apps such as Safety Assure provide a mobile and cloud based platform to aid safety managers in this endeavor. Functions such as Incident Management provides employees with a way to efficiently report potential hazards or accidents, the incident will be logged according to OSHA compliance standards and streamlines the reporting process for the employees, making the lives of the safety managers and employees easier.
-
Review and Improve Safety Plans
Health and safety, like many business processes, is constantly evolving and updating. As businesses look for new and innovative ways to operate new potential hazards will arise. It is the responsibility of a safety manager to ensure that companies are always up to date with their safety plans. Improved safety standards will be achieved through regular audits, asset maintenance and continues training. Occupational health and safety applications will often be used frequently during this stage in order to compile robust reports on the progress made.
An overview of the responsibilities held by safety managers can seem overwhelming, however with the right personality and assistance from some of the facility management and health and safety applications available companies will be reaping the benefits associated with a safer and more productive facility.
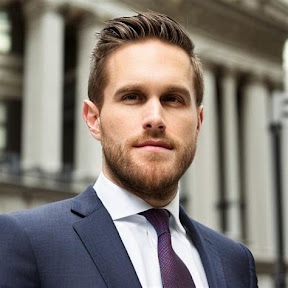
Darren Trumbler is a versatile content writer specializing in B2B technology, marketing strategies, and wellness. With a knack for breaking down complex topics into engaging, easy-to-understand narratives, Darren helps businesses communicate effectively with their audiences.
Over the years, Darren has crafted high-impact content for diverse industries, from tech startups to established enterprises, focusing on thought leadership articles, blog posts, and marketing collateral that drive results. Beyond his professional expertise, he is passionate about wellness and enjoys writing about strategies for achieving balance in work and life.
When he’s not creating compelling content, Darren can be found exploring the latest tech innovations, reading up on marketing trends, or advocating for a healthier lifestyle.